The naming for horizontal pouch machines is a little perplexing. On most horizontal form fill and seal equipment, the film runs horizontally, but the pouch is held vertically, open side up. The material is dropped into it from the top.
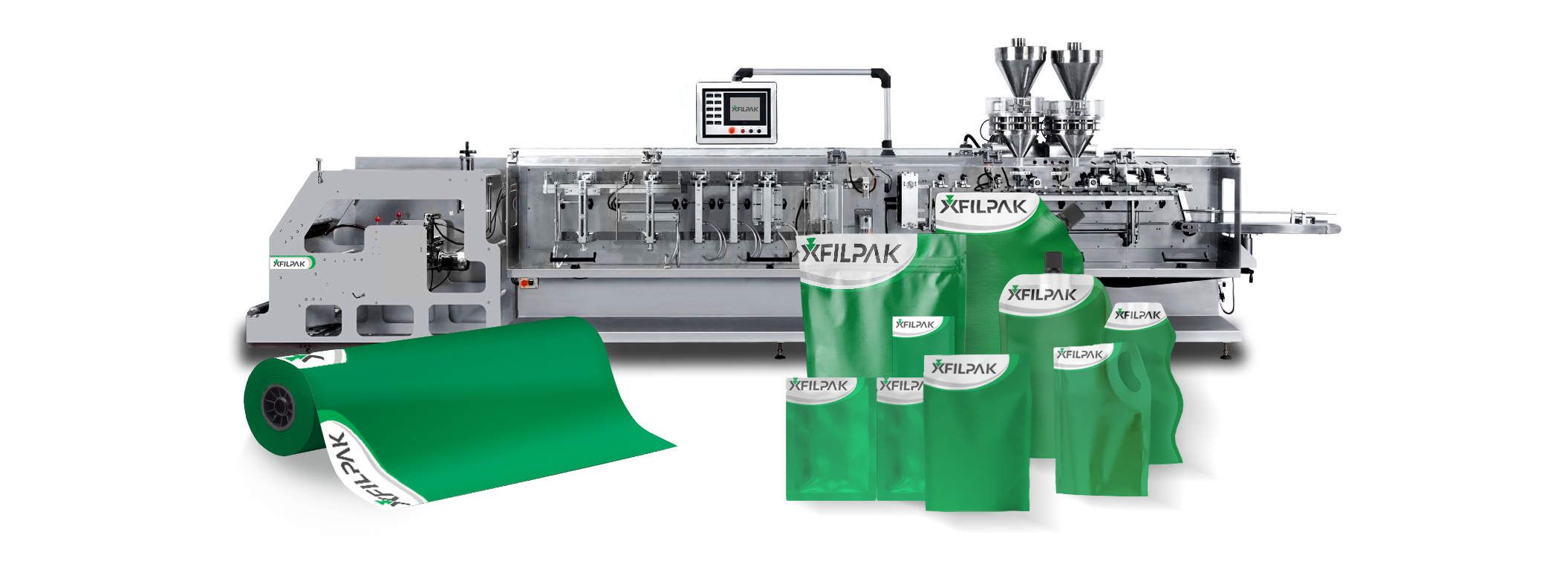
Horizontal pouch machines can handle almost any product, from soaps and detergents to chicken parts. They are identified for performing a seal on three sides of the pouch, with the fourth side formed by a fold in the film. Pouches made on this sort of machine can be basic 4-sided square and rectangular bags. These devices can also accommodate more advanced designs, such as standup bottoms, unique forms, dispensing fitments, and zipper bands.
In this scenario, the terms top and bottom may be misleading. This section will use the term "top" to relate to the top or open side of the pouch as it is being made. “the bottom” is referred to the fold side. In some cases, the printing will be reversed or even sideways, resulting in the folded side becoming the top or side in the store.
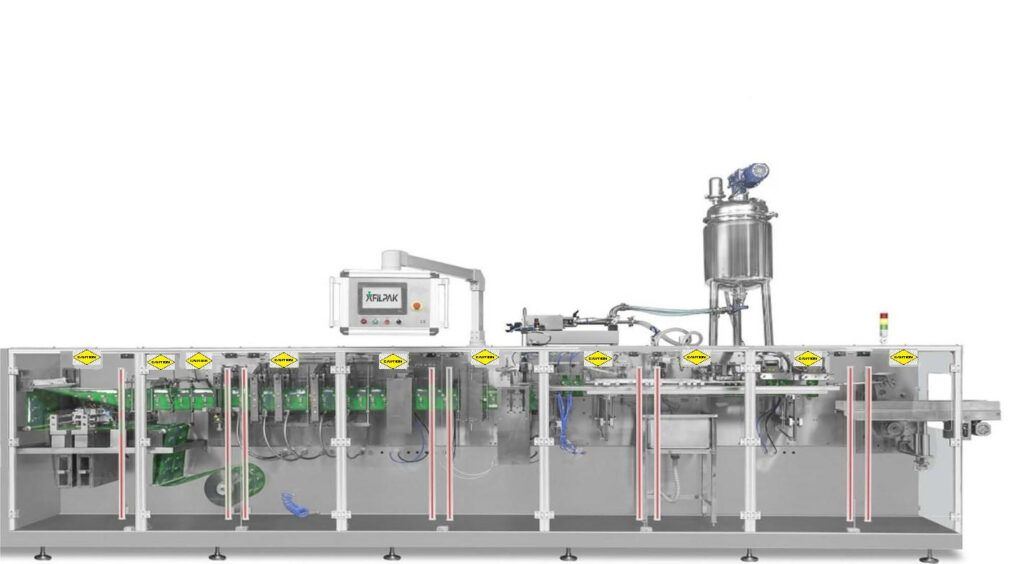
We provide sustainable solutions that are suitable to your budget in Montreal and Quebec. Contact us for a free consultation to find out about the best solution that fits your needs.
Working principle of horizontal form fill seal machine
The film is pulled from a source roll and horizontally folded in half to form a vertical "V" shape. If a standup pouch is desired, a special guide is utilized to mold the bottom of the film as it comes off the roll into something like a "W" shape. This gives the completed pouch a flat bottom, allowing it to stand freely on a storefront or consumer shelf.
At this time, zippers or tear strips for simple opening or resealing may be installed. These are fed into the bottom of the "U" lengthwise from a roll in a constant strip. The strip is welded into position on both sides of the bag by a heated sealing jaw. In certain circumstances, having the zip strip towards the top of the bag is preferable.
This is accomplished either by attaching the strip combination to one side of the bag and then welding the other side during the final sealing stage, or by welding the strip arrangement to both sides of the bag and then separating them to open the bag.
A pair of horizontal sealing jaws seals the film between the pouches after it has been shaped into the vertical trough. The pouches can be cut apart at this stage, although some designs leave them in a continuous strip for subsequent division. Some packages will include two or more bags to facilitate the packaging of various items, such as epoxy and its activator. The cutoff blade is configured to cut the required combination in these instances.
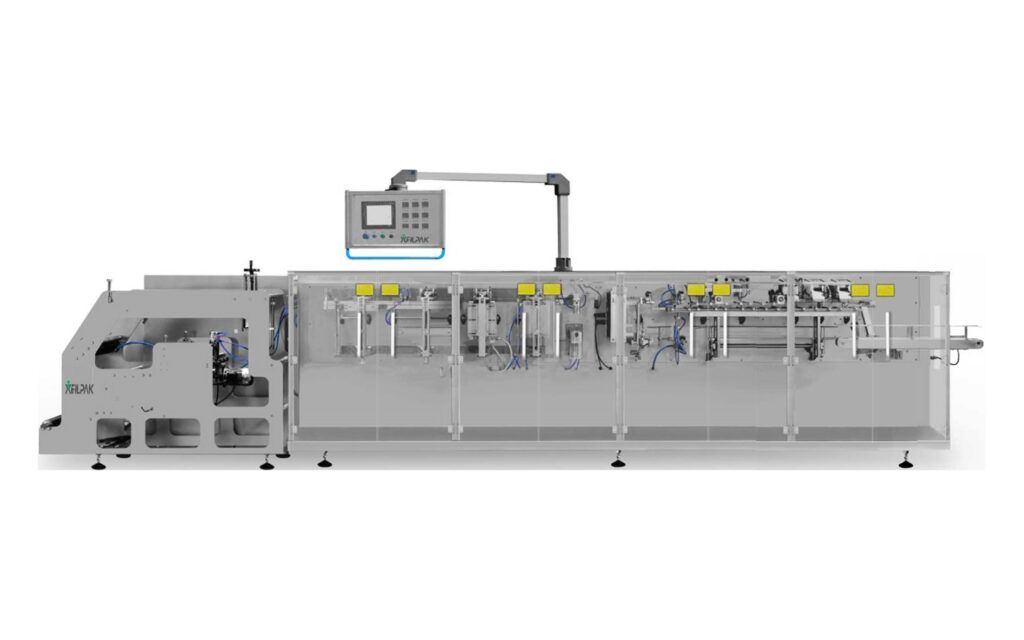
Other packaging designs may need the supply of pouches in multi-pouch strips, wherein the average consumer will tear off an individualized pouch at the time of usage. In such circumstances, a perforating blade can be used to create a tear-off hole between every pouch, and a cutoff blade can be set to cut the specific quantity of pouches into the strip. These cuts are often vertical and straight, leading in a plain square or rectangle packaging. Some packages could benefit from a more aesthetically pleasing form. To cut curves or other complicated forms, special-shaped cutting dies might be used instead of straight blades.
The bag is now sealed on two sides, with the bottom created by the materials fold and the top left open. Despite the cutoff technique, the bag will be seized by grabber fingers right before cutting and taken to the filling station for the rest of the procedure.
After being cut, the pouches are sent forward to the first filling station. As they come to the filling system, a pair of suction cups pushes the top of the bag open. Fluids, lotions, granules, or piece parts—such as sweets or chicken parts—can be filled utilizing a number of common filling methods.
In some cases, it might be required to fill two things- for instance noodle and soup powder -in the same pouch. Pre-mixing the components, installing two fillers to release into a shared filling funnel to the pouch, or employing two filling stations can all achieve this.
Filling is usually the most time-consuming part of the procedure. In some cases, using multiple filling stations might result in faster production speeds. On each cycle, these could each fill half of the necessary amount of product. The machine can also be set up to index two pouches per cycle. This allows you to fill two at once. Some machine manufacturers would partition the bags into two tracks prior to filling to attain even faster production speeds. This enables for further filling stations to be installed on the same machine.
When the pouch is full, the suction cups release it and it indexes to the closure station. Typically, this is a pair of linear, horizontal sealing jaws. If a more complicated form is needed, specially designed cutting dies and sealing jaws may be employed. Prior to sealing, a distributing tip or other fitting may be inserted in the top of the bag. A pick-and-place mechanism is used to slide the fitting into the bag opening and hold it in place. Welding the film to the fitting is accomplished using special sealing jaws. After closure, the grippers transport the pouch to the device's terminus, where it is discharged.